The Pain Relief Dosing Device Giving Patients Control
An innovative new device for administering pain relief, developed from the ground up by Akkodis engineers specialized in medical technology, can not only empower patients but also ease the workload of hospital staff.
4 minutes
6th of March, 2024
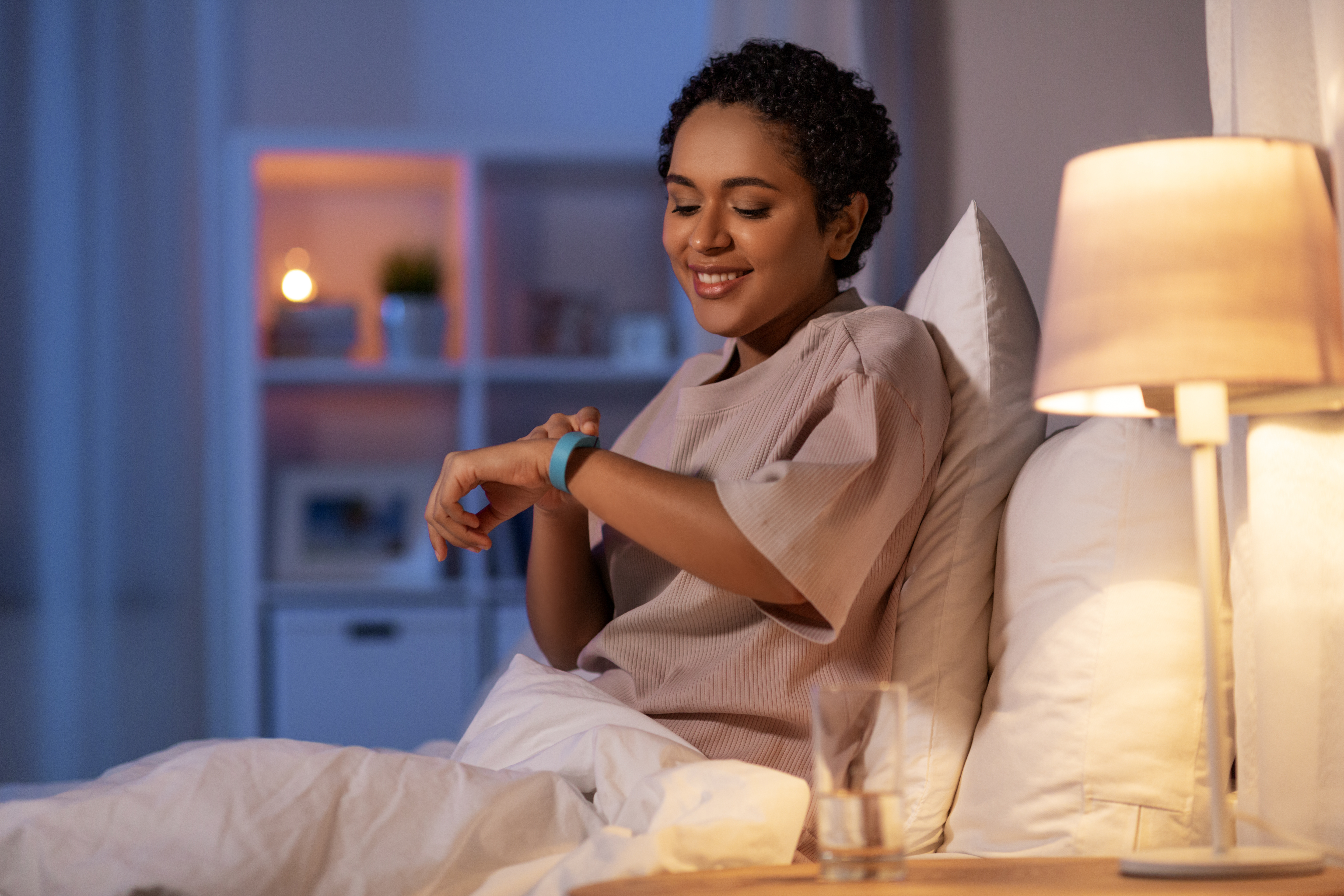
Turning innovation into reality: Inside Akkodis Medical Engineering Team
A German medical technology company came up with the idea of giving patients control over their own pain medication by way of a specially designed nasal spray. While the concept sounds simple, it was difficult to make it a reality.
Andreas Ries and his 35 colleagues at Akkodis’ Department for Medical Engineering and Mechatronics took up the challenge of helping the company get its device off the drawing board and into the hands of patients. The team, based in Mannheim and Oldenburg, Germany, specializes in combining hardware, software, mechanics and deep domain knowledge to develop medical devices and is ISO 13485 certified to work in that strictly regulated domain. “We are the ones they call to do projects nobody has done before,” says Ries, head of the team, which is made up of hardware and software developers, project managers, electronics and mechanics engineers, as well as quality management experts.
Designing from the ground up
The medical company approached Ries and his team to develop a dosage system for the nasal spray containing pain relief medicine. The device had to fulfill several requirements. It needed to be manually operated, reusable, safe, and user-friendly, both for the patients managing their own pain medicine and for hospital staff to hand out. It also had to be designed in a way that would make malfunction, misuse and overdosage impossible. It also had to comply with all rules and regulations in the area.
“We designed the device from the ground up, with extra care going into the manual operation,” Ries says. “We designed the mechanics so that even elderly and sick people have enough grip power to release a dose and the size of the device accommodates large as well as small hands.”
To ensure that the device can only be used by the patient for whom the painkiller has been prescribed, the team added a Radio Frequency Identification (RFID) wristband containing a chip that communicates with the device via Near Field Communication (NFC). “The chip authenticates the user and eliminates any misuse by others,” Ries says. “The spray flask containing the medicine can only be accessed by hospital staff, and dosage is limited to a set time interval adjusted to the patient’s needs.”
The device, of which hundreds have now been made for clinical studies, is a self-contained system not accessible from outside. It is equipped with two microprocessors and has redundant electronics, eliminating any malfunctions. As it does not transmit, there is no risk of affecting other devices, for instance, a pacemaker.
Medical machinery
While the technical attributes of the device are carefully calibrated, they proved in the end to be the most straightforward part of the project, Ries says.
“It was a huge job to fulfill all the rules and regulations for such a device and to document the entire development process in great detail. Fortunately, we have thorough quality management people on board. They are indispensable because quality, documentation, and traceability are crucial in this domain.”
The pain relief solution is far from the only project Ries and his team are working on. Using their combined expertise in hardware, software, and mechanics, the team contributes to developing a prosthesis that grows with the patient. In the past, children suffering from bone cancer faced multiple operations to get a new prosthesis fitting their height. Now, prosthetic devices can grow with the patient. Ries is developing a new type of drive technology powered by inductive energy transfer, enabling doctors to adjust the prosthesis to the growth of their patient without invasive surgery.
How Akkodis leverages company resources for tech innovation
Ries and his team are also developing new electronics for lung ventilators, laboratory equipment for in vitro diagnostics, and much more. Being part of a large company operating in a wide range of hi-tech domains helps them keep their knowledge up to date, allowing them to learn from colleagues working in more agile sectors.
“The medical device market moves more slowly than automotive or consumer electronics. There’s a new car model every year, while a heart-lung machine can be on the market for 30 years unchanged. But when customers come to us to help them develop new products, they can rest assured that they get access to state-of-the-art technologies,” Ries says.
“Our advantage comes from being part of a large company with strong internal knowledge transfer and a well-established culture of continuing education and staff development,” he says. “We may be a small unit and functioning to some extent as a company within the company for certification reasons. But when it comes to knowledge, we tap into the expertise of thousands of colleagues.”