Electrifying the Boating Industry
Akkodis’ Automotive Expertise Unveils New Horizons for Electric Boats
5 minutes
18th of August, 2023
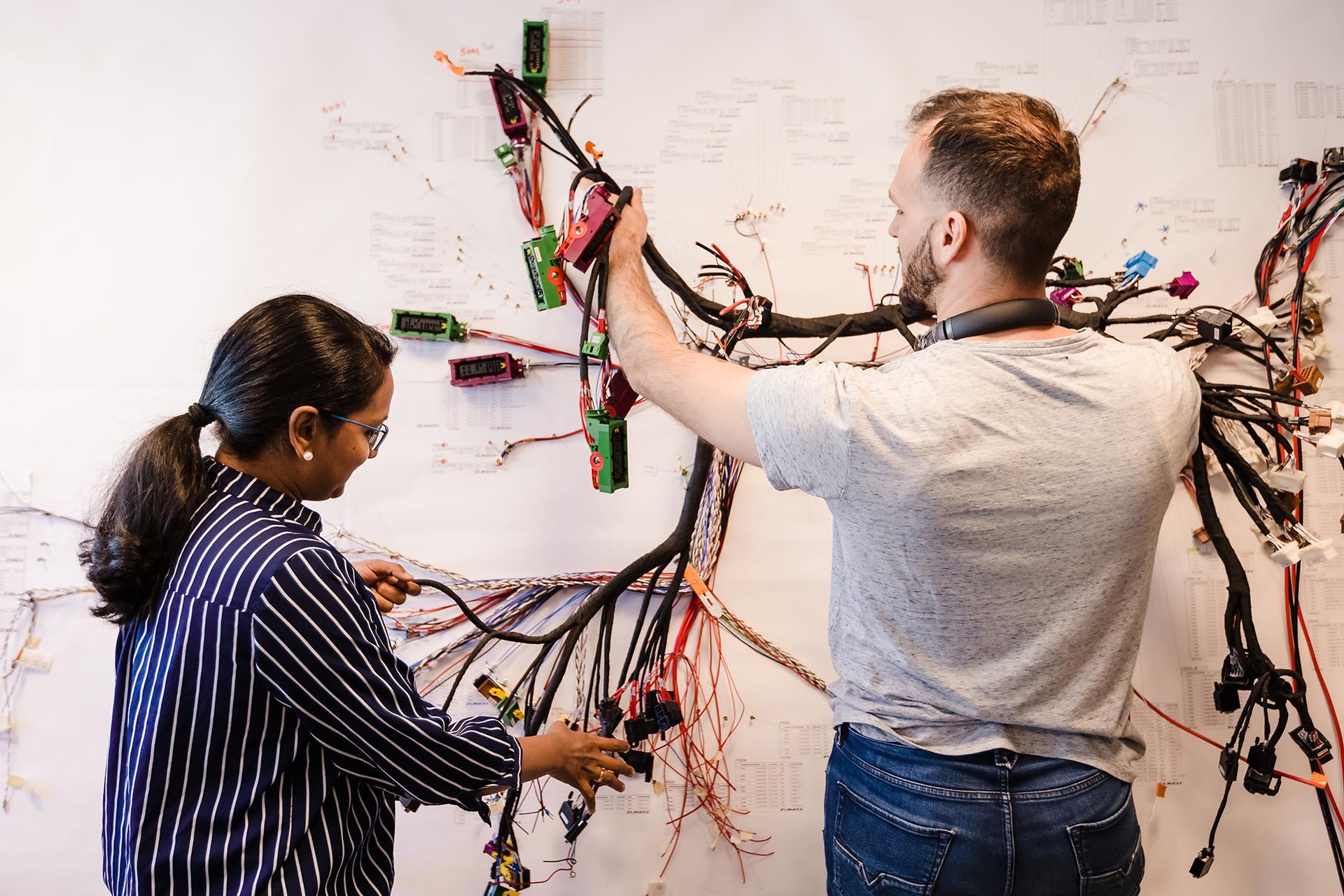
This article was originally published in Thinkers & Makers, a magazine from Akkodis featuring the smartest minds and innovative projects that are driving the future of technology and engineering.
Akkodis is sparking off a sea change, drawing on its automotive industry wire harness expertise to develop the wiring for a new hi-tech electric luxury cruiser on hydrofoils.
The Candela C-8 promises to eliminate two of the most challenging things about speed boating: Engine noise and the boat punching its way through the waves. An all-electric drivetrain eliminates the noise, while hydrofoils turn the punching into a magic carpet ride, lifting the boat out of the water for a smooth ride and a top speed of 30 knots.

The C-8 has been described as an “iPhone moment for boats” and a “Tesla on water.”
Built in 100% carbon fiber, and with a price tag starting at 290,000 euros, the C-8 may not be affordable for everyone, but nevertheless it’s a step towards the electrification of boats and ships, large and small.
Much is happening in that area, not only related to people enjoying spending their free time on water, but also development of electric ferries, and even experiments with electric container ships.
Digital Transformation on the High Seas
Per Fernlund at Akkodis in Sweden, is excited about the organization playing a part in the electrification of transport. Fernlund says Candela is an interesting company to work with since it is preparing other disruptive electrification projects such as the P-30, the world’s first electric hydrofoil shuttle ferry.
In the Stockholm area, where Fernlund is based, several other companies are working with electrification of transportation, batteries, electric motorcycles etc. New companies are popping up all the time.
“In my opinion that’s a good thing, not only for the environment. It’s good for the development of the Stockholm area and it feels great to be a part of that,” said Fernlund.
The Akkodis team of engineers have designed the wire harness of the C-8, using their expertise from the automotive industry. But the Candela assignment has posed new challenges to the team. For instance, the boat industries have their own standards to follow.
Also, the harness had to be as weight optimal as possible, to give the boat maximum range per battery charge, as well as for the environmental impact and for cost-saving reasons. On the other hand, what made the job easier was the fact that a luxury cruiser offers more room for cables than for instance the tight spaces in a truck cabin.
Building Prototypes
Doing the wire harness for a boat has been a first for Akkodis in Sweden. Another new addition to the service portfolio has been the building of prototypes, which began about a year and a half ago.
“Before that we focused solely on working as R&D consultants. Still, that’s what we usually do: designing and developing a wire harness and leaving it to someone else to build it. But now we can also build prototype harnesses, and we can do several iterations and optimize the harness along the way. That means we can deliver a final harness design that is thoroughly tested and in a shorter time,” said Fernlund.
From Hand Built to Volume Production
According to Fernlund, Akkodis normally works for large industrial companies with a lot of powerful manufacturing machinery. Candela, however, is a young company which up until now has produced hand-built harnesses. For this setup, Akkodis’ own prototype workshop has manufactured several prototype harnesses. Also, they’ve helped Candela get ready for volume production.
“Previously, when the boats were built mostly by hand, it took weeks to install the harness. We have been working on bringing installation time down to a few hours, because that’s what’s needed when you increase production volume,” Fernlund explains.
“Moreover, as we know the market well, we’ve helped Candela find good and trustworthy harness suppliers. We sent a data package with all details out to several cable harness suppliers for quotes. After a couple of weeks with questions, discussions and presentations, Candela decided to collaborate with one of them to optimize and deliver harnesses during the industrialization phase of production.”
Workshop Training
Fernlund says working in the prototype workshop and assembling wire harnesses based on computer generated designs is an extremely rewarding training exercise for the Akkodis engineers.
With wire harnesses, you can’t do everything in the computer. Because cables behave differently in reality and are exposed to the surroundings in ways that are hard to see in the 3D world, you must do physical testing as well. Also, there is much manual labor involved in production of a harness.
“There is a lot of craftsmanship to it, and on top of that, wire harnesses come with thousands of small variations.

So, our in-house workshop is good for our customers, and good for us internally as well. It stops us from becoming too theoretical, and we learn a lot about all the tiny details that are so important in this line of work.”
Fernlund is hoping that Akkodis will get the opportunity to continue the working relationship with Candela. And, most of all, he’s looking forward to test ride the C-8.